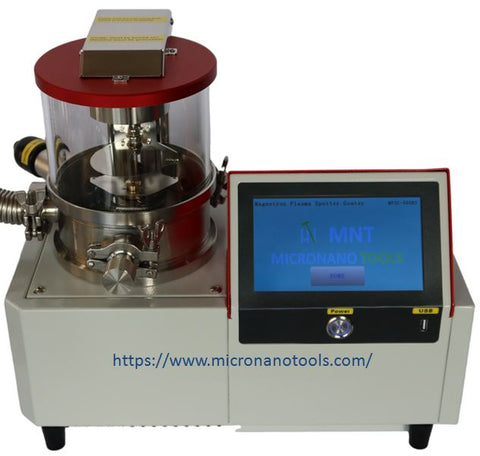
High-power Magnetron Plasma Sputter Coater MPSC-500RS, 500mA, Rotatable SH and option for thickness control
This price is only available upon request. Contact us for a quote or fill the request form at the bottom of this page.
General Introduction
The MPSC-500RS is a high-power (up to 500mA sputtering current) Magnetron Plasma Sputter Coater designed for depositing various conductive metal films for device prototyping across diverse fields and for SEM sample preparation. This robust system can sputter-coat common materials like gold, platinum, indium, palladium, and silver, as well as more challenging metals such as nickel, aluminum, copper, titanium, and cobalt. It is a powerful high-performance magnetron plasma sputter capable of coating at vacuum levels of 1 Pa or lower. The original metallic color of the coating can be preserved when used in conjunction with a turbo molecular pump.
Key features of the MPSC-500RS include high sputter power, a rotatable sample holder, real-time monitoring of sputtering current and voltage, a programmable sputter process, an electrically controlled shutter, and adjustable sample height.
Optionally, the MPSC-500RS can be equipped with a high-precision quartz crystal thickness monitor. This allows for real-time measurement and monitoring of deposition thickness by detecting changes in the crystal's oscillating frequency. The sputter process automatically terminates upon reaching the desired pre-set thickness.
A user-friendly 7-inch touchscreen interface provides precise process control, real-time feedback of sputtering current and voltage, control of the rotatable substrate stage, and operation of the electric shutter.
The MPSC-500RS is a turn-key solution and ships complete with all necessary accessories for immediate operation, including a vacuum pump with a stainless steel bellow hose, one sputtering head with a copper sputter target (copper cathode), KF 25 flanges, and a vapor mist trap.
MicroNano Tools offers a wide range of sputter targets for this plasma sputter coater. Please click here for further details.
Features
-
· High-power sputter coater with a maximum sputtering current of 500 mA
· Rotatable substrate stage (0–5 RPM) for enhanced coating uniformity
· Robust vacuum chamber combining stainless steel and quartz glass for durability and reduced contamination
· Real-time monitoring of sputtering voltage and current for precise process control
· Uniquely designed electric shutter with programmable timing control—ideal for high-purity coatings and sputtering of easily oxidized metals
· Built-in vacuum gauge for continuous process monitoring
· Adjustable sputtering current to accommodate various metal coatings, including gold, platinum, indium, silver, copper, aluminum, and more
· Standard KF hinge clamps used for all major vacuum connections to ensure leak-free operation
· Optional high-precision quartz crystal thickness monitor for real-time deposition thickness measurement and automatic process termination when the target thickness is reached
Specifications
Magnetron Plasma Sputter Coater MPSC-500RS |
|
Input power |
110V, 60 HZ or 208-240V, 50HZ, ≤1000W |
Coating program |
Pre-sputter time (with shutter), sputter coating time, and sputter current, and sample holder rotation speed, option for sputter thickness control. |
Max Sputtering Voltage |
DC -1000V; |
Monitoring |
Real time sputter voltage and current |
Max Sputtering Current |
500mA |
Target (upper electrode) |
Diameter: 50mm |
Rotation speed |
0-5 RPM |
Vacuum chamber |
Quartz and Stainless steel, φ160xH160mm |
Touch screen |
7 inch |
Shutter control |
Electric |
Vacuum reachable |
Rotary pump≤ 5 Pa; molecular pump ≤ 0.005 Pa |
Working vacuum |
≤ 5 Pa |
Substrate to target distance |
40-105mm |
Vacuum gauge |
Pirani vacuum gauge (Measuring range: 10E5Pa to 1E-1Pa) |
Overall dimension |
270×440×400mm |
Inlet and outlet ports |
KF25 vacuum outlet, KF16 air release, 6mm air inlet |
Mechanical Vacuum pump |
Option for Molecular Pump |
Input power |
AC 110V/60HZ 400W, Optional for 220/50HZ |
Displacement speed |
60HZ: 1.3L/S (4.8M3/h); 50HZ: 1.1L/S (4M3/h) |
Max vacuum |
≤ 5X10-2 Pa |
Noise |
≤ 52dB |
Control |
Integrated with the main unit or stand alone |
Flange |
KF25, Adapters available upon request |
For details of vacuum pump, please click here.
The rotatable sample holder, electric shutter, and quartz crystal seat are shown in the following picture
The high precision quartz crystal thickness measuring system is shown in the following picture.
Warranty
- Two year standard warranty with life-time support; contact for details.
- Damage due to improper storage condition or maintenance is not covered by warranty
- Longer time warranty available upon request
- Client reference available upon request
Frequently Asked Questions
1. Working principle of MPSC-500RS High Power Magnetron Plasma Sputter Coater
John S. Chapin invented the first planar magnetron sputtering source in 1974 as schematically shown in the following picture based on conventional diode sputtering. Different from the original DC plasma sputter coater, magnetic field is introduced on surface of the target to improve deposition rate while reduce the substrate temperature increase by constraining the electrons in the area on surface of the target. The magnetron plasma sputtering process may be summarized in the following steps..
2. Does distance between sample and target play any role for coating?
Yes, the distance between substrate and target can be adjusted between 40 and 105mm.
3. How to estimate coating thickness?
The coating thickness mainly depends on target material, sputtering current, and coating time. Their relation can be described approximately by the following equation:
H=M.I.T,
where H is the coated film thickness; M is material constant, when using Argon gas, approximately 0.17 for Au at a working distance of 50mm (distance between sample and target), 0.09 for Pt, 0.10 for Al (Aluminum); I is the sputtering current, mA; T is the time, second.
When using Argon or Nitrogen, 10mA sputtering current, coating gold for 100S, the film thickness will be about 0.17x10x100=170Å. When using air sputtering, M is about 0.07 for gold. The above equation is for estimation only.
4. Is the sputtering voltage adjustable?
Yes. Sputter current can be set between 0mA and 500mA. Real time sputter current and sputter voltage are displayed on touch screen screen.